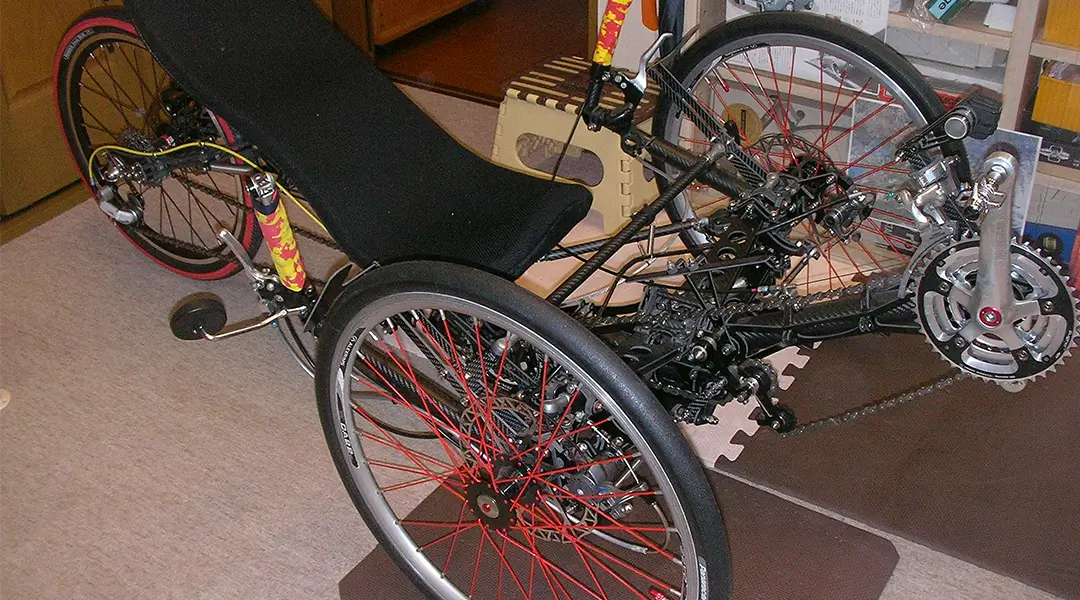
今回はリカンベントトライクのパーツにCFRPを採用した【N 様】にカーボンラボ.jpの導入の成果についてお話をお伺いしました。
- 導入前の課題
- アルミ材だと後処理を含めコストがかかる
- 他素材だと形状的に作れない制限がある
- 加工依頼のための三角法での図面が大変
- 重量が重くなり機動性が低くなる
- カーボンラボを選んだ理由
- 見積もり対応も早くスタッフが丁寧
- 価格面にも納得できた
- サイトで加工の制約等を説明されている
- 導入後の成果・効果
- アルミ材と比べると加工コストダウンできた
- 三角法的な正式図面が必要ないので楽
- 車両の重量もアルミに比べて半分近くなった
カーボン製作事例リカンベントトライクの補強パーツにカーボンを採用
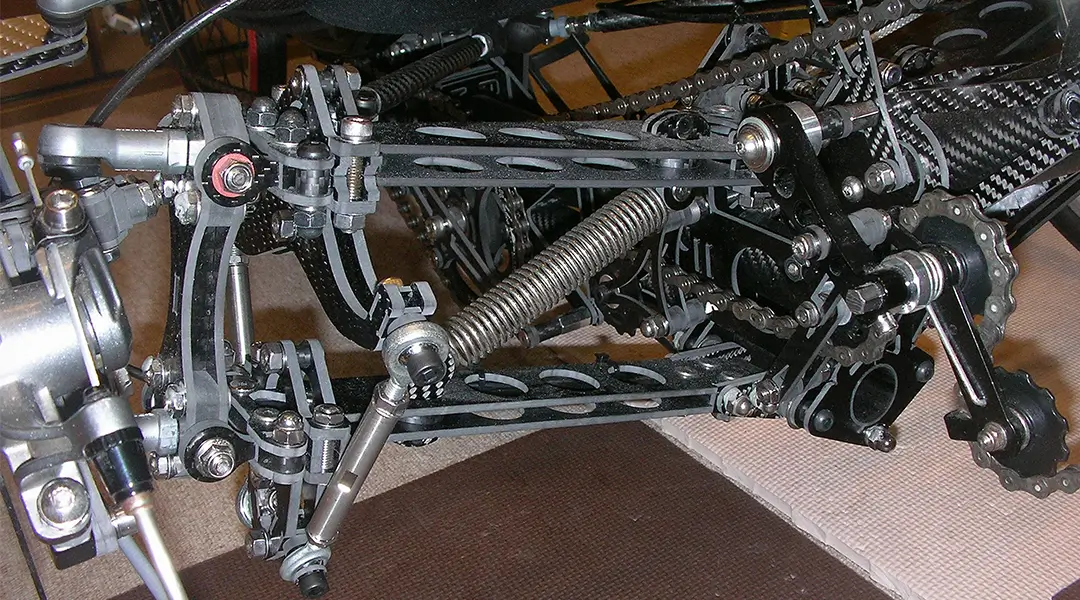
今回製作したカーボンパーツの用途は何ですか
今まで御社に数回注文してきましたが、今回のは、今年初めに製作したリカンベントトライクのフロントサス周りのねじり剛性があまりに小さかったので、これを改造、補強するための追加パーツです。
アマチュアの自設計なので、組みあがってみないと、構造的な剛性、特にたわみ剛性、捻り剛性が機能的に必要なレベルまで確保されているかどうかわかりません。
単純に言えば、カーボン材は高強度なので、アルミ材で作るより部材厚を薄くできます。薄くなるということは、たわみ易くなります。
アルミなら板一枚でたわみ剛性が確保できる場合でも、薄いカーボン材なら立体的にしないとたわみ剛性が出ません。
カーボン素材を採用した理由はなぜですか
元々はアルミ材で作っていたのですが、カーボン材はアルミよりはるかに高強度なので、アルミでは無理な小さく複雑な形状でも簡単に作れます。
またアルミではできない中空構造的な立体物も、カーボンならプレート材を重ね合わせる事で実現できます。
構造的な剛性を確保するためにはどのような形にすれば良いかを考えるのですが、アマチュアなので立体構造物の剛性計算ができません。
強度自体は素材が高強度なので詳細な計算ができなくても、まず強度不足になるということはないのですが、剛性については試行錯誤的になり易いです。
試行となると、アルミよりはるかに低加工コストのカーボンでしかできません。
製作したカーボンパーツの品質はどうでしたか
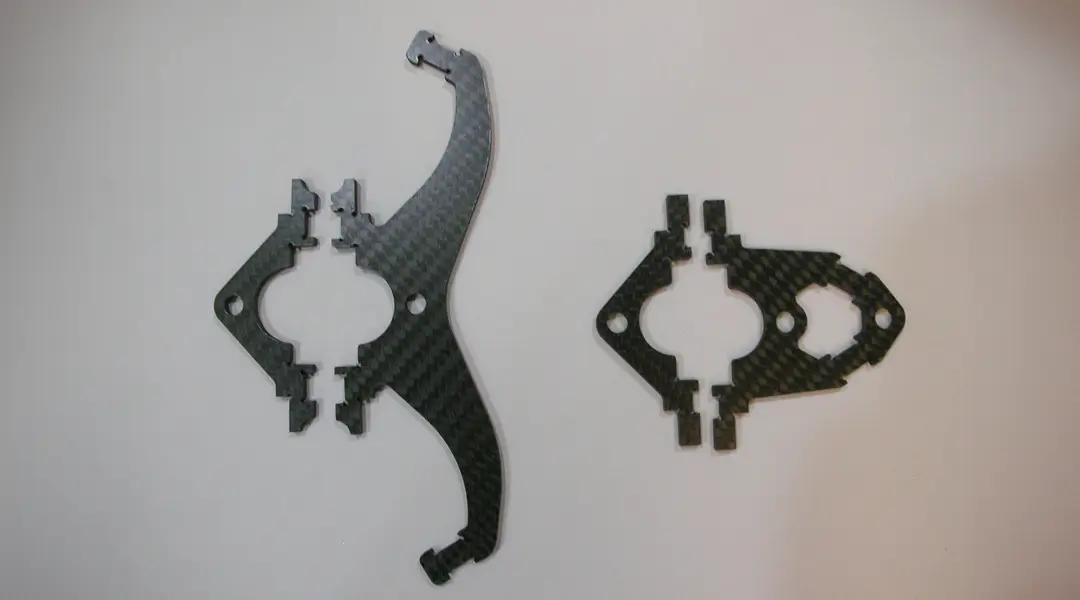
実際には許容誤差以下の精度で加工されています。
例えば4mm厚プレートを井桁状に直交させる場合、スリット幅を4mmで加工すると実際には4mm厚プレートは差し込めません。カーボン材は硬いのでスリットが長いとまず無理です。
この場合スリット幅を+0.25mm(0.125+0.125mm)で図面を描いておくとOKです。穴あけ加工の場合も一緒です。φ8mmパイプを通したいなら、半径4.125mmの円にしておけば差し込めます。
加工寸法の公差±0.3mmと記載されていますが、実際には±0.125mmまでは精度確保されていました。
導入前の課題加工コストが高額かつ車体が重くなり機動性が低くなった
カーボンラボ.jp導入前の課題はどういったものがありましたか
アルミ材で作っていた時は、加工コストがかなり高額になりました。一品加工に近いこと、加工したあとに腐食防止のためアルマイト処理が必要になること等によります。
さらには、
- 自分で追加加工ができない、形状的に作れないという制限も生じる
- 各パーツ図面(加工依頼のための)を三角法で描くのが大変
- 車体として組み上げた場合、全体重量が重くなりすぎて機動性が低くなった
という課題がありました。
カーボンラボを選んだ理由対応のスピードも早く、価格も納得できる
カーボンラボ.jpに発注した決め⼿をお聞かせください
以下のような決め手がありました。
- 注文や見積もりの対応スピードが早い
- スタッフの対応も丁寧で迅速
- 見積もりの価格も納得できる
- カーボン加工の柔軟性、制約等も詳しく説明されている
導入後の成果・効果加工コストも下げられ車体重量も軽くなった
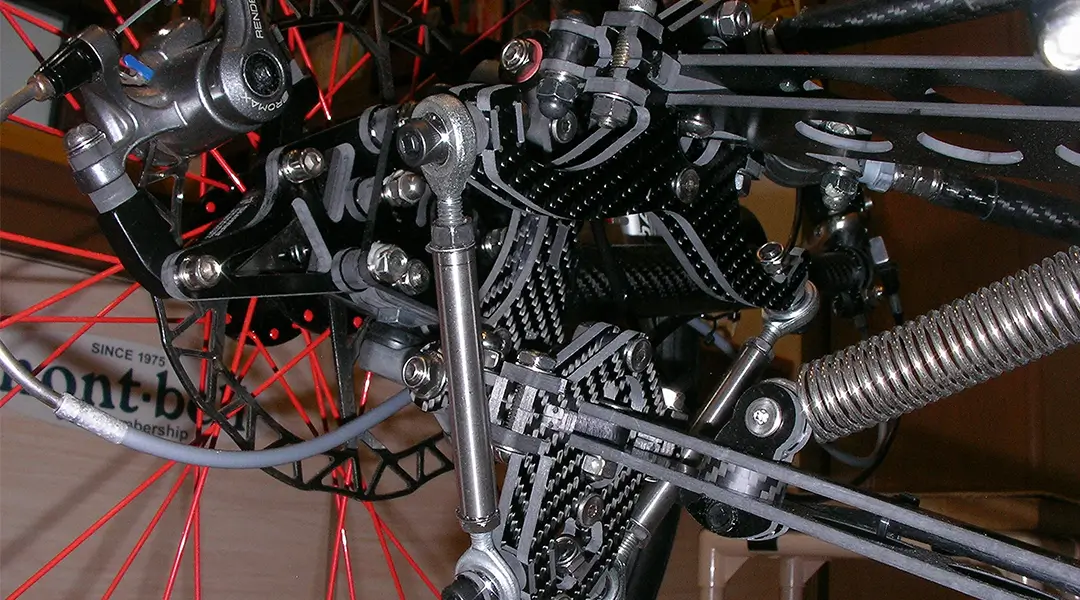
導入後は課題が解決できましたか?また弊社に改善して欲しい点はありましたか?
加工コストは、もともと安価なのをさらに部材取りを工夫し、使用板厚を2~3種類にまとめればかなり低額になり、アルミ材に比べれば1/2~1/3以下にすることができました。
パーツ形状もプレートの組み合わせ方(切込、重ね合わせ方)を考えることによってかなり自由自在なものが可能です。
図面も最終的には線画だけでいいので、三角法的な正式図面は必要ないので楽です。
また、完成全体重量もアルミ材に比べて半分近くになりました。
今回製作されたパーツの注文内容
注文方法 | カーボン板(データ入稿) |
---|---|
プリプレグ | 標準(クロス) |
表面織組織 | 標準(綾織) |
表面仕上げ | 標準(マット加工) |
納品までの日数 | 発注から17日で発送 |
ご利用いただいたサービス
お見積りの流れ
- STEP1お見積りフォームから製作するパーツ情報を送信する
- STEP2最短当日~3営業日以内にお見積り書をメールで送信します
- STEP3お見積り内容に満足頂ければ、メールにて発注の連絡を下さい
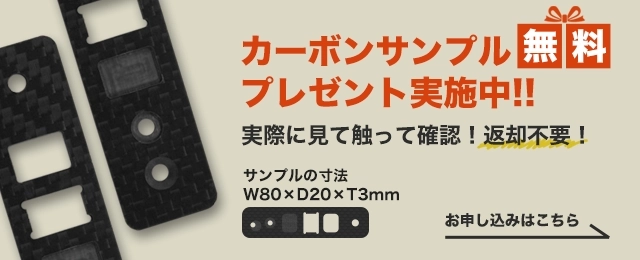